液態硅膠制品常見問題及解決方法對策
瀏覽:888 發布日期:2018-07-09 14:46:06
一.制品固化不完全
(1)溫度太低
液態硅膠一般是鉑金硫化,硫化溫度一般在110℃~150℃之間,(因硅膠原料和產品結構不同硫化溫度略有差異)
對策:檢測模溫(以實際測量為準),適當提高模溫。
(2)硫化時間太短
液態硅膠硫化時間一般在60S~300S之間,(因硅膠原料和產品結構不同硫化時間差異較大,以實際情況為準)
對策:適當延長硫化時間。
(3)注料管道或模具有污染
有些油脂類污染物會破壞液態硅膠的硫化結構。例如機臺潤滑油和模具上的防銹油以及工人手上的汗液油脂都會影響液態硅膠的硫化
對策:清洗注料管道,清潔模具。要求工人戴指套或手套操作。
(4)混料不均
液態硅膠都是A/B劑雙組份,硫化成型前要充分混合均勻。
對策:盡量使用品牌廠商的混料系統,調整攪拌器的轉速和壓力。
(5)膠料太冷
有些公司在暫時不生產時,為了延長膠料使用期限,往往會把已混好的膠料冷藏存儲,等再使用時直接加入生產。
對策:冷藏存儲的膠料需在室溫下放置一段時間在使用。
(6)內嵌物料溫度過低(塑膠或五金)
這主要是針對包膠產品,特別是內嵌較厚的產品,車間溫度又低(主要是冬季)
對策:預熱內嵌物件。
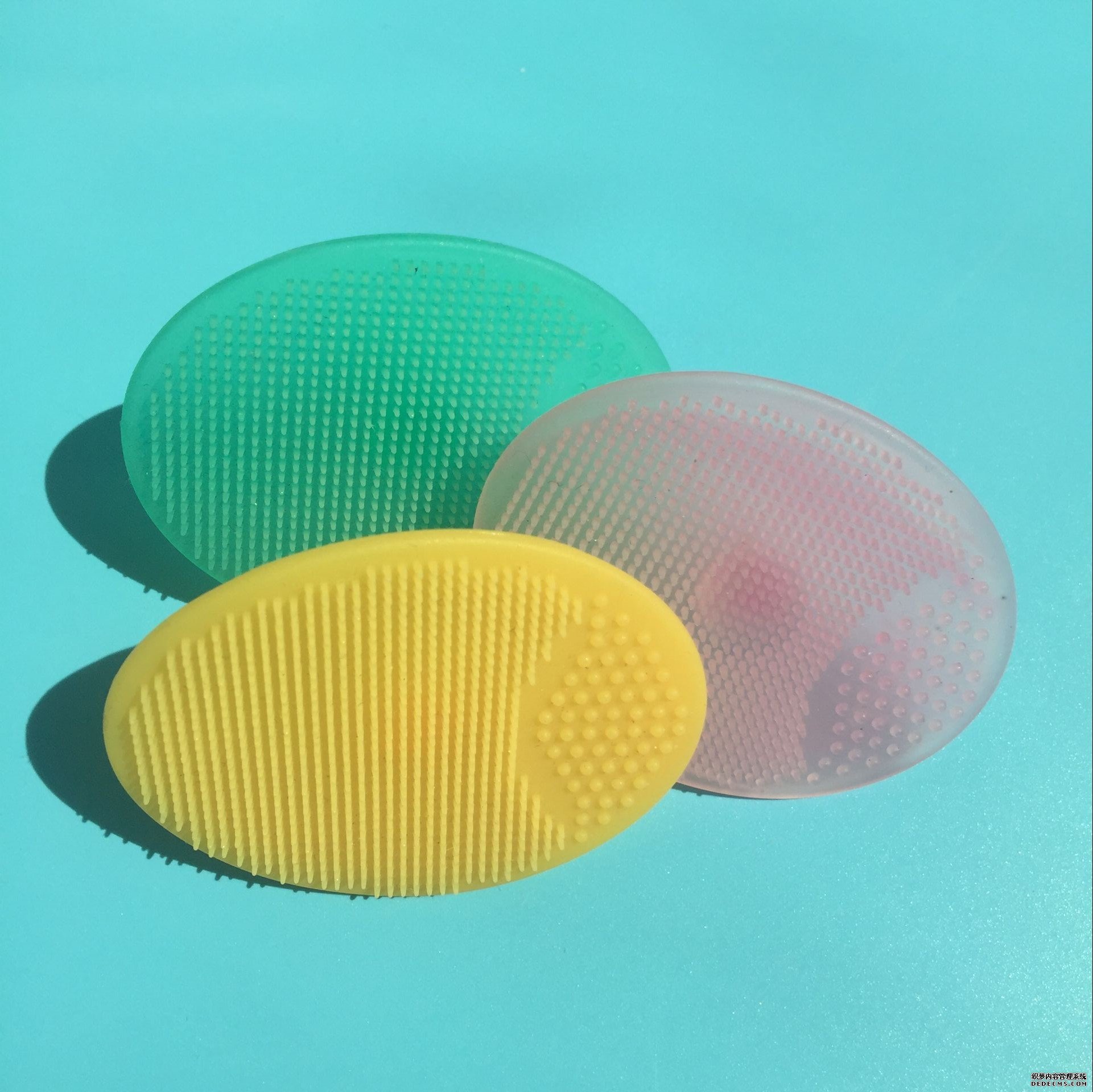
二:產品表面不熟(或局部不熟)
(1)脫模劑有問題
液態硅膠有很多種型號,既使是同一型號不同廠家硅膠性能也會有差異,使用的脫模也有不一樣。一般是使用含硅類的脫模劑,具體以廠家推薦的為準。
對策:更換脫模劑
(2)模具表面有污染
在生產時可能有油脂類的污染物沾在模具上(防銹油,機臺潤滑油或工人手指汗液)
對策:用甲苯清洗模具。
(3)內嵌物件(塑膠/五金)有污染
有些內嵌物件(塑膠/五金)在生產過程會沾有灰塵油脂之類的臟污,后續工序又沒處理干凈。
對策:成型之前一定要將內嵌物件清洗干凈,烘干后再生產。
(4)空氣污染
液態硅膠制品在生產過程中一般要用到氣壓(氣槍)脫模,若空壓機內的氣體不干凈,很容易把臟污噴到模具上影響制品。
對策:檢查氣路,清潔或更換空壓機過濾器和干燥器。
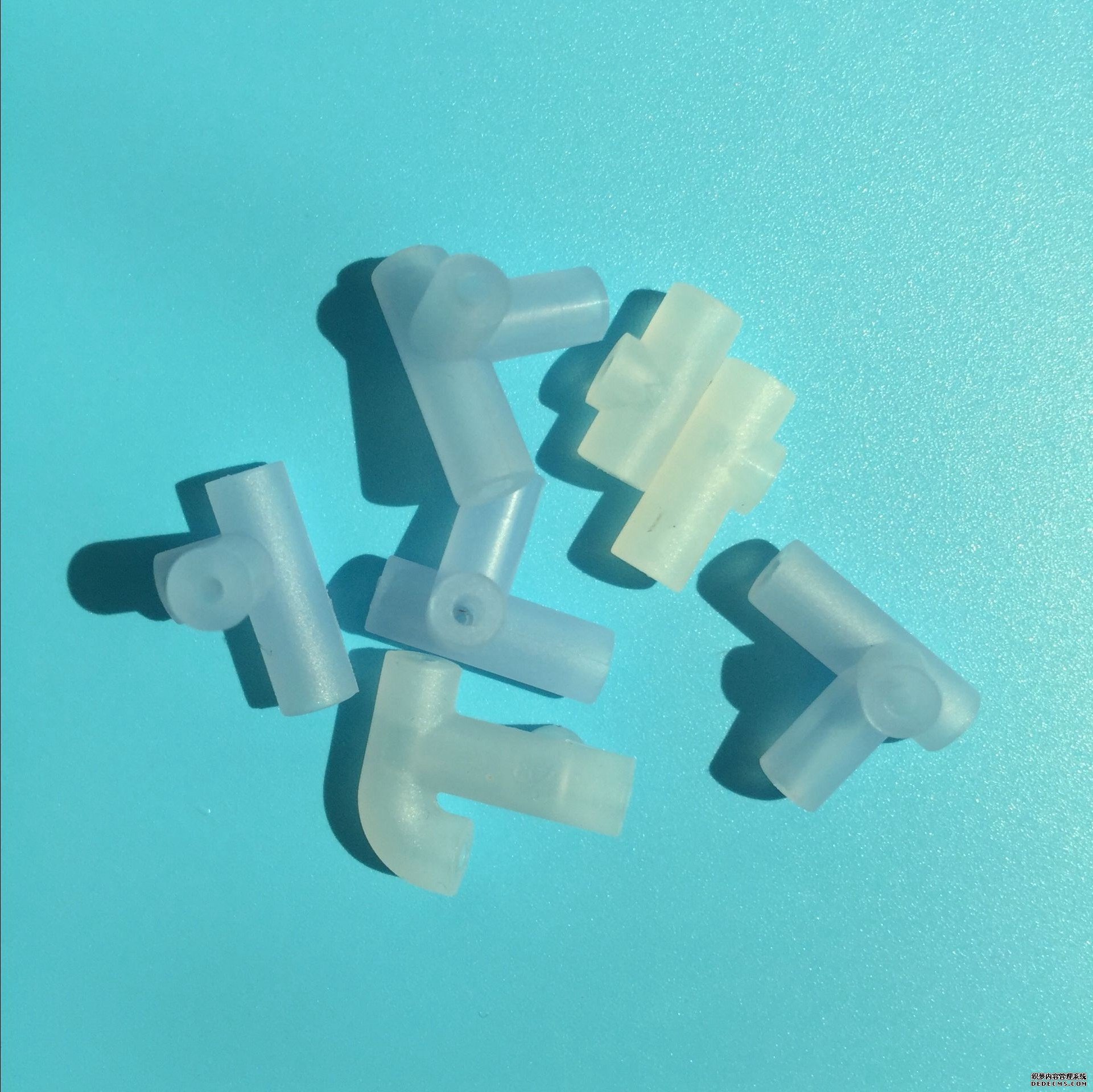
三:產品有雜質(或色斑)
(1)膠料或模具有臟污
對策:清洗模具,用干凈膠料生產。
(2)操作員所用手套,氣槍有臟污
對策:定期更換手套、氣槍套管。
(3)膠料混合不均
在生產中有時會發現在制品中有白色透明狀的微小凝膠粒,這一般都是膠料沒有充分混合均勻所致
對策:調整攪拌器轉速和背壓,必要時可增加混煉工序(液態硅膠專用混煉機)
(4)色漿混合不均(或色漿分散、沉淀)
各廠家的硅膠成份不同,所用色漿也會有差異,最好使用膠料廠家配套的色漿。
對策:更換色漿。
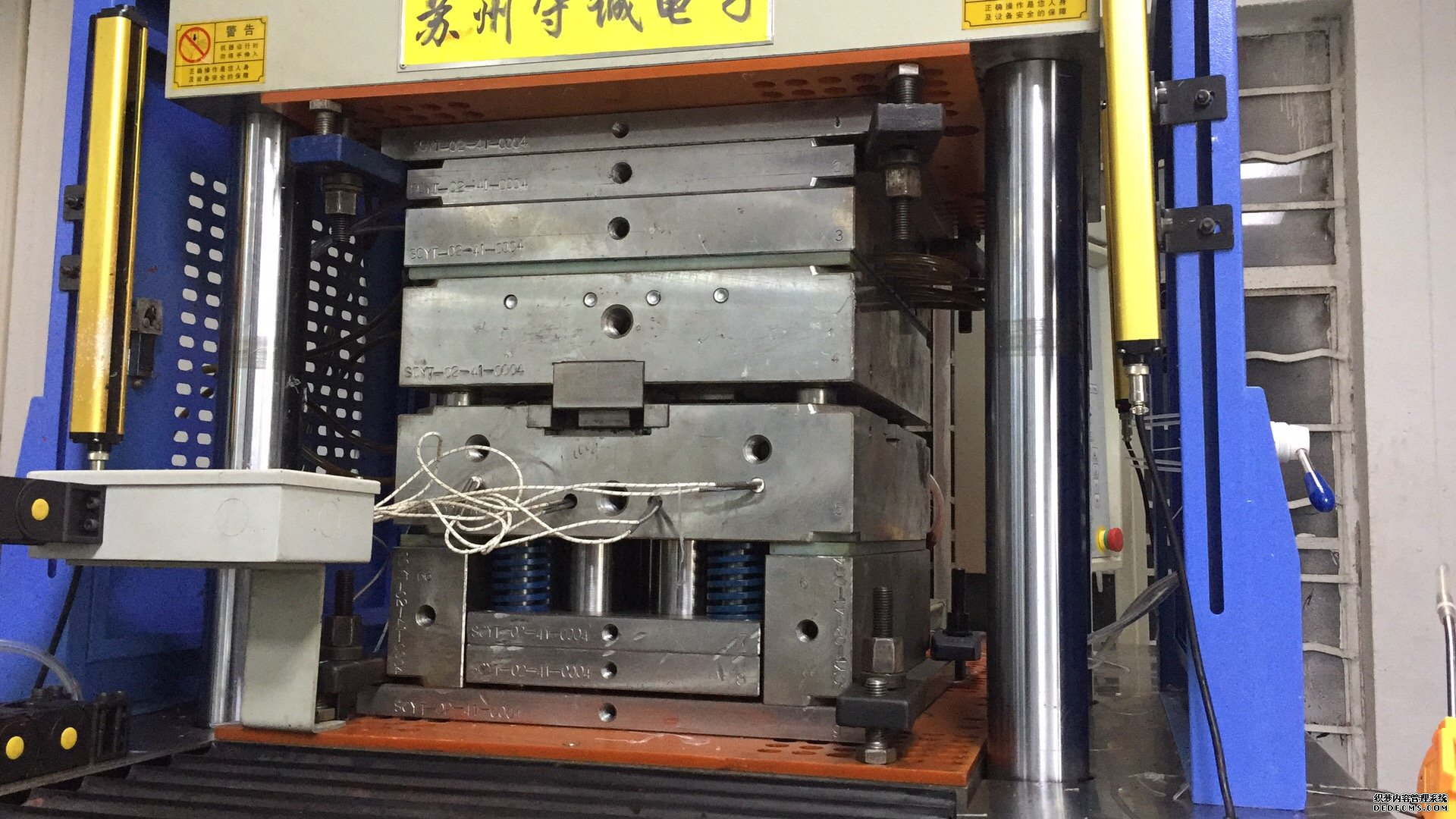
四.產品變形或縮水(包膠類的硅膠制品最容易發生這種問題)
(1)內嵌物件形變溫度過低。
液態硅膠的硫化成型溫度一般在110℃~150℃之間,所以內嵌物件的形變溫度至少要在150℃以上。
對策:更換內嵌物件的原材料,采用耐高溫材料。
(2)內嵌物件受壓力不均導致變形
硅膠包膠產品的內嵌物件需要在模內有穩定可靠的定位,封膠位需承受一定的模壓力,所以受力部位一定要均衡。
對策:調整內嵌物件的受力部位。
(3)產品結構設計不合理
硅膠縮水率一般比內嵌物件(塑膠/五金)大,包膠產品的硅膠部分結構盡量要均勻,不可局部太厚或太薄。
對策:建議客戶修改產品結構。
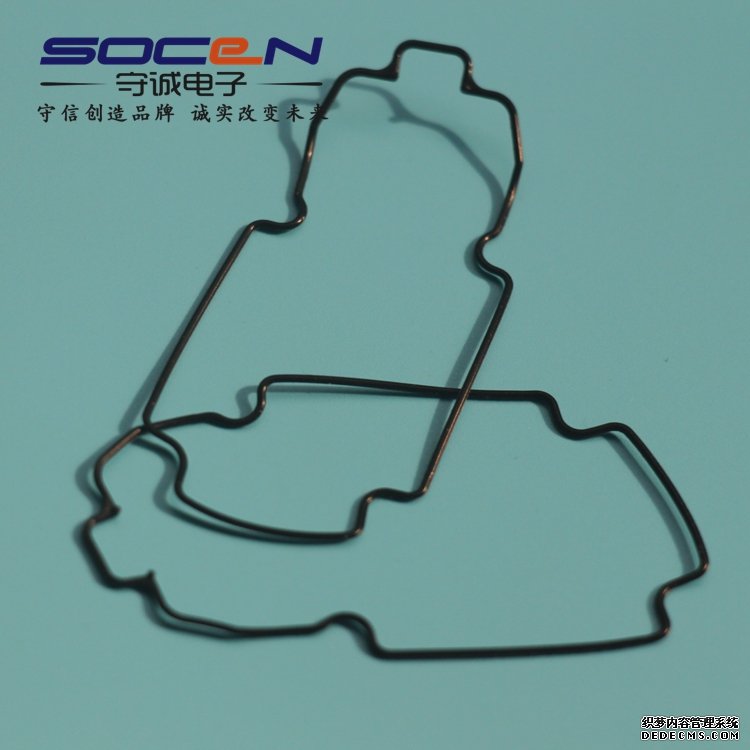
(五)產品缺料、凹痕
(1)供料不足
對策:調整注料量,增大注膠壓力。
(2)注膠口太小
液態模的注膠口一般設計為1.0~1.5為佳,但有時也受硅膠原料硬度和粘度影響,可適當增大注膠口,以實際為準。
對策:增大注膠口。
(3)排氣不良
排氣結構設計不合理也會造成產品缺料,其實是因為氣泡在產品表面破裂所致。
對策:合理設計排氣結構,增大排氣口,必要時設計模內抽真空。
(4)模具表面臟物
一旦模具表面粘有臟物,會造成批量性的不良。所以生產中產品要定期抽檢。
對策:清潔模具。
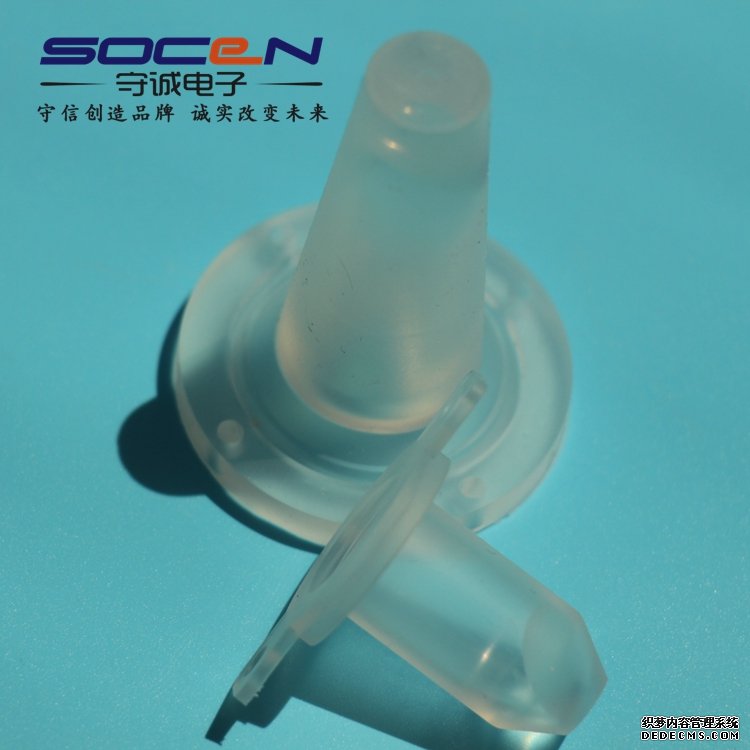
六.產品有氣泡(困氣)
(1)排氣不良
一般是排氣結構設計不合理,排氣位置應設計在產品的末端。
對策:調整排氣位置。必要時設計模內抽真空。
(2)膠料里有氣
一般是在膠料混和的時候產生的,有些粘度較大的硅膠料也容易產生氣泡。若是手動混料,最好是放置沉淀一段時間。
對策:檢查攪拌混料器是否鎖緊。必要時增加混煉工序(液態硅膠專用混煉機)
(3)注膠口設計不合理
有些較大的硅膠制品,為改善膠料填充,往往會設計多個注膠口。以我個人的經驗,盡量只設計一個注膠口是最好的。硅膠原料雖然看起來很粘稠,實際上流動性很好,一般不用擔心填充問題。若一定要設計多個注膠口,注膠口的位置一定要均衡對稱,并在相對應的位置設計排氣口.
對策:調整注膠口位置。
七:產品有飛邊(溢料)
(1)供料過量
對策:減小注膠量,降低注射壓力,加大鎖模力。
(2)模具分型面精度不足(或磨損)
液態硅膠因為流動性好,溢流值只有幾個µ,所以模具加工精度要很高。有的廠家為控制產品飛邊,采用微量注塑技術。這種方法對那些較大產品尚可,而對微小型產品效果就不是很理想。為解決微小型制品飛邊問題,可以在產品末端增加溢料槽。
對策:提高模具加工精度、提高機臺微量注膠精度、增加溢料槽
(3)模具自拆磨損
這是針對自拆結構產品。有些產品自拆結構較薄弱,容易磨損。
對策:合理設計自拆結構。模具表面電鍍,增加模具硬度。
八:產品沾接不良(主要是針對包膠類產品)
(1)內嵌物件有臟污
對策:成型之前把內嵌物件清洗干凈,烘干。
(2)粘接劑有問題(底涂)
一般硅膠都不能直接與塑膠、五金、玻璃粘合,成型之前需做底涂(粘接劑),現在市場上各種粘接劑名目繁多,效果也各不相同。現在市場也有自粘硅膠,成型時無需做底涂,但由于這種自粘硅膠價格較高,粘接效果和底涂工藝也還有差距,對模具表面處理也有要求,目前應用還不是很廣。
對策:更換粘接劑。必要時可以考慮改為自粘硅膠。
(3)脫模劑有問題
有些脫模劑會和粘接劑發生化學反應,會使粘接劑失效。所以一般做包膠類的產品盡量不用或少用脫模劑,一定要用也要噴脫模劑半小時以后再生產。
對策:更換脫模劑。模具做表面處理改善脫模。
(4)產品結構設計不合理
有些包膠類的產品在結構設計時由于沒有考慮到后續生產工藝,給后續量產帶來很大的麻煩,嚴重影響產品質量和交期。所以產品前期開發評估很重要,一定要充分考慮產品量產的可能性。
關于包膠類產品的結構設計可參考我前期發布的《防水件產品結構設計個人建議》。
對策:建議客戶修改產品結構。
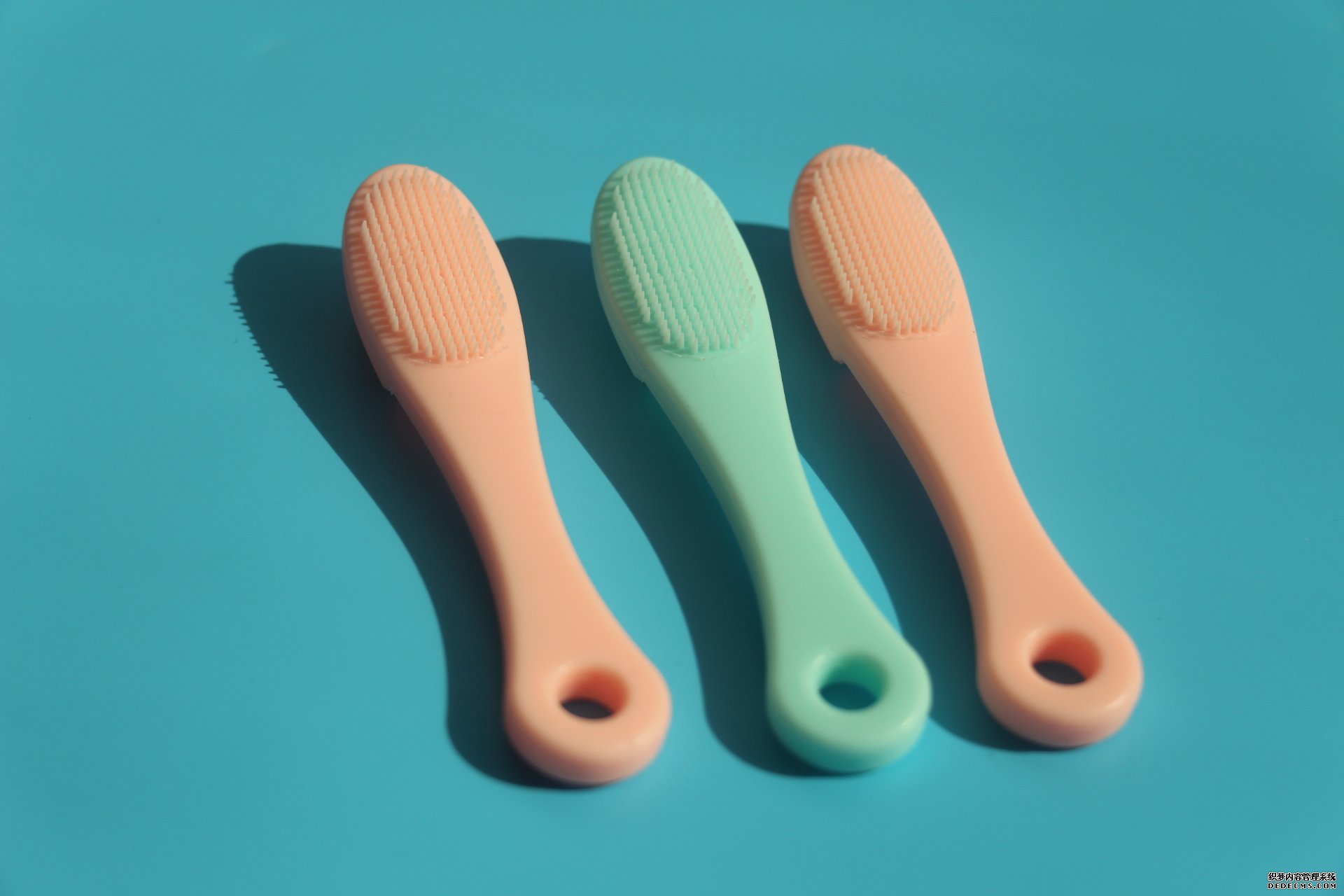
蘇州守誠電子有限公司是一家致力于液態硅膠醫療配件,液態硅膠汽車配件等液態硅膠制品廠家 專注定制生產液態硅膠制品22年歡迎致電0512-66704180
蘇州守誠電子有限公司是一家致力于液態硅膠醫療配件,液態硅膠汽車配件等液態硅膠制品廠家 專注定制生產液態硅膠制品22年歡迎致電0512-66704180